Not just a dressmaker...
1st July 2016
Thirty years of experience in various roles in fashion and clothing have resulted in me being able to provide the service that I do. The term dressmaker/seamstress is one which seems to reduce what I do to just sewing, I am actually more than just a dressmaker! Although, yes, I sew dresses, that is only a small part of it...
I refer back to a time when probably every woman would sew their own clothes and make repairs to their own clothes, or pay for a seamstress to do it, but times have changed. Apart from the recent resurgence in the interest of dressmaking due to certain tv shows, most clothes are mass produced, even high end designer garments that command the highest prices are mostly factory made. These days most garments are massed produced and one factory worker would be responsible for one process repeated on hundreds of garments each day, for example, one person would just sew the zips in, this is known as piece work. The only garments made by hand now days would be couture, bespoke garments and men's tailored garments that are hand made, from start to finish by one person a tailor or seamstress/ dressmaker and finished with care and attention to detail, also, rightly commanding the high prices that goes with the specialised service. Below are just some of the details of my particular work as a bespoke dressmaker.
DESIGNER
Making a bespoke garment or a one off, couture garment can be quite a lengthy process and one that involves a variety of skills practised over many years. I start with the design process and designing a suitable and desirable garment for the client. I always aim to make something beautiful that is wearable, that is why I love making garments, it's a kind of art using fabrics.
It all starts with needing to be a clear communicator and trying to assess what your client is actually visualising, I may be sketching an idea as my client is explaining what they want. Many things need to be taken into consideration in the design process. Sometimes the client has a design in mind and obviously I have to respect this, although I need to be able to give my opinion as to whether this will work for them or not. Some of my clients have fitting issues with high street clothes and want something made that will fit them correctly. I have clients who want a specific design and cannot find this on the high street, where as others just want the luxury of having something made for them or have a special occasion and want to look and feel special, without the worry of showing up in the same dress as another guest! If I am designing for the client, I need to show them a selection of designs then we can then discuss what they would like made. A non- refundable deposit is required before any design work can even start and you will see before I even pick up my scissors I have many tasks to complete. It is useful that a customer has a good idea of what really suits them, for example colours, styles to suit their body shape, what suits their personality, what they will feel comfortable in and if it is appropriate for the occasion, as a lot of work will go into making the garment and it has to be right.
The first initial consultation should set out what the client wants made and the design either decided upon and a deposit paid if work is to commence, a set of measurements taken and a time frame of fittings established with time allowed for any unforeseen circumstances.
PATTERN / GRADER / TOILER
Once a design has been chosen, I will take a set of measurements from the client, correctly fitting under garments need to be worn for me to get accurate measurements and the shoes for the correct height if necessary. Next I will arrange to see them for their first toile fitting, a toile being a mock up of the finished garment in a similar but cheap version of the final fabric. From the measurements taken I will then draft a block pattern, not use a shop bought pattern, which is a first basic shape. Next I will use that block to then create the actual style required as a paper pattern. A pattern cutter is a highly skilled position within the clothing indusrty, who works closely with the designer to achieve the required look and fit of the garment and usually has to train for several years to work independently. Some pattern cutters can also grade which means sizing up the original size, usually an 8, into larger sizes, however, when making a bespoke garment I am switching between pattern cutter and grader to create an individual size to fit just one persons body exactly. This is arguably one of the most difficult parts of my job, as everyone is so different! I would then source and buy a cheaper substitute fabric for a first toile which should give a good resemblance to how the style will work when finished. Next I need to cut the cheap substitute fabric out using the pattern I have drafted and then sew it together accurately and press it, but without finishing it entirely as that is not required, as this garment is not going to be worn other than for a fitting. A toile is going to be the mockup or prototype of the finished garment, in which the fit of the garment is corrected and the style is adjusted if needed. If any fitting or style changes are required at this point, I will then adjust the paper pattern and the toile. If there are sufficient enough changes to be made, then a second toile will be made and again fitted until this is correct. It is important for the client to know that any major style changes made after the first toile is made will result in extra costs being added to the final price, due to the required time spent on making changes.
SOURCING SPECIALIST
Next I need to make a follow up appointment with the customer and fabric is either bought by the client on my advice, giving them an accurate measurement for what is required or I have been asked to source usually a choice of fabrics for them. I have to make sure that I provide a good selection of fabric samples in various colours, types and weights and also know what price range they are considering. Buying the correct fabric is obviously very crucial, I would not want to spoil the whole design by using a cheap fabric that does not hang or drape as expected, but equally it is not necessary have to pay a huge amount to make a beautiful garment! Another thing to remember is the colour of the fabric, whether or not it suits the client's complexion and flatters them, after all I want them to look amazing in one of my dresses! The chosen fabric then needs to be tested on the sewing machine with the thread to make sure it sews nicely and will press flat. The machine needle also has to be the correct one for the type of fabric, for example , I could not use a leather needle on a chiffon as it would pull and spoil the fabric! I also need to identify wash care instructions for the customer as some special fabrics may only be hand wash or dry cleanable and the iron guidlines are needed too. The other important thing to remember is the other items that may be needed to finish the garment, so I will need to source threads, zips, linings, buttons, fastenings or trimmings, for example a beaded applique piece that may be required for the front of a dress.
SAMPLE CUTTER
When it is time to cut the fabric I need to make sure my cutting table is clean and clear of clutter, then I need to work out the best way to lay the fabric and how to be as economical as possible. This I usually worked out before I order fabric as I need an accurate measurement to know how much to buy, although I add a small allowance for any faults that may be in the cut length of fabric. Laying up the fabric may be quite straight-forward, however if I am cutting a print that needs to be matched or a lace with a scallop edge, the pattern pieces need to be placed in a careful manner to suit the design of the garment. Matching a design when laying the top and underneath layers of fabric and cutting slippery fabric is also a challenge. A good pair of tailors shears is required for cutting neatly as I do not want to cut leaving any jagged edges as this will affect the finished garment by cutting into the seam allowance. I have also to make sure I do not mix up cut fabric pieces or lose track of the right and wrong sides of the fabric as this could be time consuming trying to unpick or re-cut pieces.
DRESSMAKER
For a first toile fitting, I need at least an hour for me to check not only the fit and hang of the garment, but to make sure the look of the design and the proportions are correct on the client, remember that I have translated a sketch into a flat pattern and then into to a three dimentional toile and some times things are nearly 100% right first time but sometimes one or two more fittings are required depending on the body shape and complexity of the style being made. Only once the client is completely satisfied with the fit and style of the toile will any fabric be purchased and then cut. Next I have to make the rest of the pattern pieces, for example linings and facings in which to finish the garment in a good quality way. The way the garment is finished off can make all the difference to the look of the whole garment, for example making sure there are no threads hanging, it is beautifully pressed, the seams are neatened cleanly and lined if required.I then still need to source trimmings and linings for the garment, so for example zips, buttons interlinings and matching threads. Once all is all done, I can then cut the actual fabric using the corrected pattern and start assembling all the various components of the garment on the sewing machine. Sometimes hand tacking is required first dependining on the fabris or pattern shapes used. Sample cutting or cutting out individual garments, is in itself a job in the fashion industry and is a very skilled position especially if the fabric that is being cut is fine and slippery. Making one garment from start to finish would be the job of a sample machinist in a fashion studio and the machinist would have to work closely with the pattern cutter, who would help with advising the machinist on how to put the garment pieces together in the correct way and how the garment needs to be finished. Sewing a garment can take several hours and sometimes many hours due to the fabric or style. When machining especially, I need a high degree of precision and concentration to sew bespoke garments, especially when operating my industrial sewing machine, accidents could happen if I did not focus properly! Machining various processes is an accumulated skill, for instance, I am able to sew a zip into a dress, that is one proccess, I can make a shirt collar, that is another proccess, but there a many different proccesses which make up garments and years of sewing experience produces this skills set. As I am sewing, it is important to underpress the garment each time I sew a new proccess so that the fabric lays flat when it is finished. I also use various attchments to my machine for different functions such as a zip foot.
Fishing garments in the correct way for the type of fabric or style of the garment is a skill in itself and a poorly finished garment can spoil the whole garment. Lining garments adds a quality to the garment but also lengthens the life or wear of the garment.
PRESSER AND FINISHER
The first thing to do is press or hand sew in any interlinings or stiffening materials required and then start joining all the pieces together by machine. There is an order of how I need to construct the garment depending on the style. As each bespoke garment is totally unique, it takes longer to make as I have to figure out the best way to assemble that particular garment, as I am not remaking one style over again as a factory garment is made. Each process in a factory would be repeated by one machinist at a fast pace, this is called piece work. I have to consider which process will need to be done at each stage for the best outcome. Next I decide to how finish the inner seams to stop them fraying, this has to be done in the way that will best suit the thickness of the fabric, so for example if it is a silk lightweight dress then I would join the garment together with french seams. I next join in any facings, zips and linings. Some degree of hand finishing is also required which is also a skill which has to be observed and not used widely in everyday manufacturing.
Once the garment is completed and top pressed I then hang it and cover it to keep it clean and crisp for the client. I usually finish the garment completely before I arrange a final fitting of the garment. Usually the garment is perfect and the final payment is paid, although there may still be minor changes to be made.
It is important to have a good understanding of my clients needs, keep up with current trends and to be flexible, as I never know what is going to happen from day to day and every customer is unique! The process of making a unique garment or outfit is labour intensive and therefore can be costly, however it is a worthwhile investment and the resulting garment will be one to treasure and hopefully be worn over and over again! Many skills are involved in creating a bespoke garment and therefore I am not just a dressmaker!
Gallery
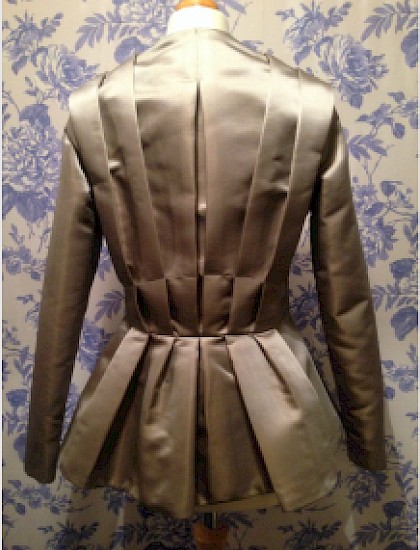
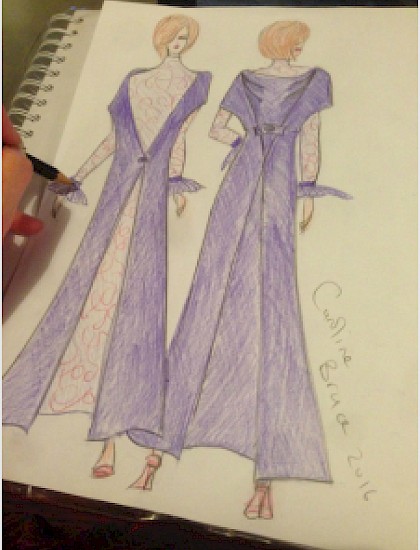
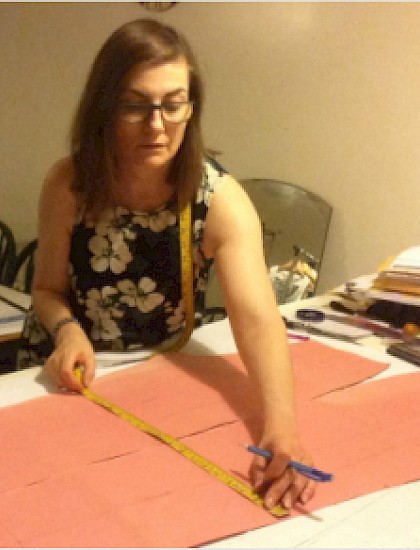
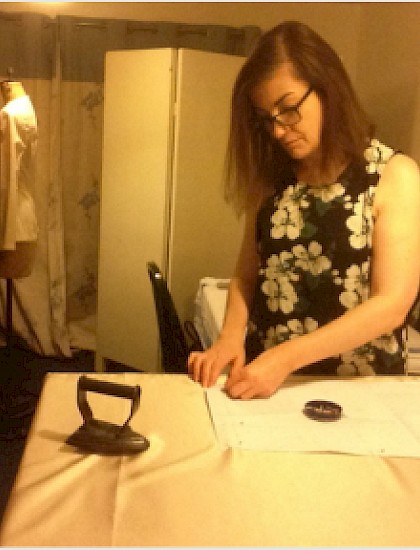
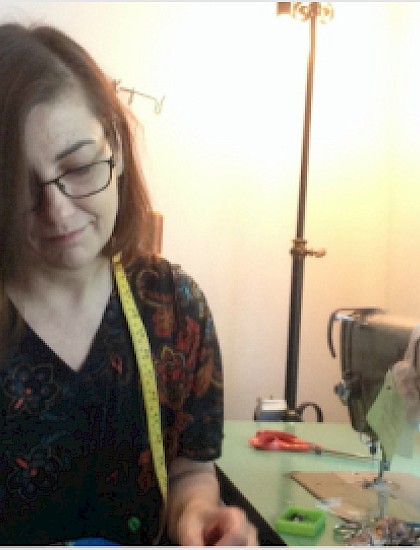
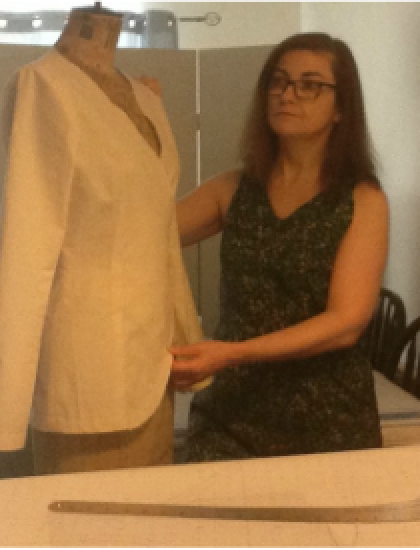